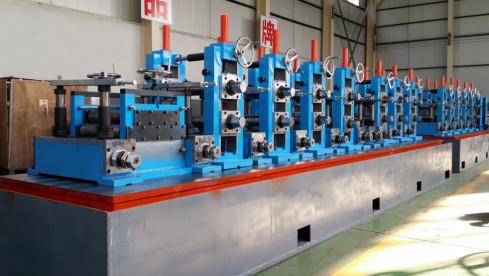


Erw Tube Mill Layout
-
Payment
-
Origin
China Mainland
-
Minimum Order
1
-
Packing
Pieces
- Contact Now Start Order
- Description
Product Detail
Quotation
1. Price for Equipments
Sr. | Equipment Description | FOB Xingang Port Price (USD) |
Double Head Uncoiler | 178,000 | |
2 | Shear and Manual welder | |
3 | Spiral accumulator | |
4 | Forming and sizing section | |
5 |
200KW Solid State H.F. Welder with Electrical control | |
6 | Friction saw | |
7 | Conveyor, Roll out Table(12m) And Basket |
Price Exclusion:
1 | Saw blade | 1 piece |
2 | Clamp used on saw | 1 set |
3 | Outside burr scraping insert | 2 pieces |
4 | Tools to change the rollers | 1 set |
Price Exclusion:
Foundation construction |
Installation of the equipment |
All the connections from the power source, air source and water source to each of the machines. |
Necessary material, equipment and tooling for the assembly and running of the machines, including air compressor, water pump, channels and vent stacks for the exhaust of the gaseous products, prelaid pipes for foundation construction, cable channels, etc. |
Tools and instruments for the site assembling, installation and commissioning. |
Consumables such as impeders and oil. |
All the protections required safety rules, such as covers for the ditches, guide rails, passing bridges, etc. |
2. Price for Service:
Validity of Quotation: Quotation is remain valid within 3 months.
PROPOSAL FOR TUBE MILL
1. GENERAL DESCRIPTION
The proposed tube mill is a combination of equipment installed in a line for the production of High Frequency Induction Welded (HFIW) carbon steel tubes. The process involved is cold forming of carbon steel strip in circular shapes, longitudinal welding, sizing, converting into specified shape and cutting to pre determined length.
The complete line is divided in three sections:
? Entry Section
? Forming, welding, Cooling and sizing Section
? Cutting and Delivery Section
Raw material (Steel Strip) in form of a coil is uncoiled and fed into forming section passing through the equipment of entry section. Entry section enables the tube mill to run continuously by using strip joining and accumulation equipment. Tube is formed in round shape passing through a set of driven and idler rollers of forming section before welding. In welding section tube id longitudinally welded by using high frequency induction welding method. Outside bead is removed and formed in shape of scrap. The weld seam is ironed and tube passes though the cooling section. In sizing section, tube is formed to specified size and converted into specified shape. After sizing, tube is cut to specified size and converted into specified shape. After sizing, tube is cut to specified length by using flying cutting equipment and delivered in collecting though passing through run out conveyor.
1. BASIC DESIGN DATA
Design of the proposed line is based on following specification:
? Raw Material Specification
Sr | Service | Price (USD) |
1 | Commission and Training | USD 50 /day /person |
The Buyer shall pay for the international air tickets and the local, such as board and lodging, daily transportation, communication,Insurance, etc. |
Validity of Quotation: Quotation is remain valid within 3 months.
PROPOSAL FOR TUBE MILL
1. GENERAL DESCRIPTION
The proposed tube mill is a combination of equipment installed in a line for the production of High Frequency Induction Welded (HFIW) carbon steel tubes. The process involved is cold forming of carbon steel strip in circular shapes, longitudinal welding, sizing, converting into specified shape and cutting to pre determined length.
The complete line is divided in three sections:
? Entry Section
? Forming, welding, Cooling and sizing Section
? Cutting and Delivery Section
Raw material (Steel Strip) in form of a coil is uncoiled and fed into forming section passing through the equipment of entry section. Entry section enables the tube mill to run continuously by using strip joining and accumulation equipment. Tube is formed in round shape passing through a set of driven and idler rollers of forming section before welding. In welding section tube id longitudinally welded by using high frequency induction welding method. Outside bead is removed and formed in shape of scrap. The weld seam is ironed and tube passes though the cooling section. In sizing section, tube is formed to specified size and converted into specified shape. After sizing, tube is cut to specified size and converted into specified shape. After sizing, tube is cut to specified length by using flying cutting equipment and delivered in collecting though passing through run out conveyor.
1. BASIC DESIGN DATA
Design of the proposed line is based on following specification:
? Raw Material Specification
Raw Material Feeding | CR bright tube with oiled, Galvanized steel, HR coil |
Material Tensile Strength | Max 500MPa |
Material Yield Strength | Max 235MPa |
Coil OD | 800mm to 1500mm |
Coil ID | 508mm&610mm (customer order) |
Coil Weight | Max 3000 kg |
Strip Width | Min 200mm, Max520mm |
Strip Thickness | Min1.0Max 3.0 mm |
? Production Range
Type of production | ?Round Tubes ?Square and Rectangular Hollow Sections |
Round Tube OD | Min 63.5 mm, Max 168mm |
Round Tube Thickness | Min 1.0mm, Max 3.0mm |
Square Hollow Section | Min 50x50mm, Max 130x130mm |
Rectangular Hollow Section | Min 40x60mm, Max 100x150mm |
Square and rectangle Tube Thickness | Min 1.0mm, Max 3.0mm |
Tube Cut Length | Min 5 meter, Max 8 meter |
? Line Specification
Line speed | Max 50m/min Min 10m/min |
Direction of Operation (To be confirmed by buyer) | Left ? Right or Left ? Right |
Welding Method | High Frequency Induction Welding |
Total Electric installed capacity | 600kw |
Line area | Approx. 40x5.0 meter (length x width) |
? Required Utilities and working Conditions(Buyer's Responsibility)
Driven power | 3 phase AC380V±10%,50Hz±1.0% |
Control power | 1 phase AC220V±10%,50Hz±1.0% |
HF welder use water cooling tank | 20 m³ |
Tube mill use water cooling tank | 20 m³ |
Circulating water pressure | 0.5~ 0.6 Mpa |
Air compressor exhaust | =1 m³/min |
Air compressor pressure | 0.4~0.6 MPa |
Air source | =3 m³ |
Over head Crane | 5 tons Over head Crane 2 sets |
2. The technical flow of the production line
{Steel Tape}?? Double-head Uncoiler??Strip-head Cutter and welder??Spiral accumulator??Forming section(Flattening unit +Main driving unit +Forming unit +Guide unit +High frequency induction welding unit +squeeze roller)+ De-burr frame ??Cooling unit ?? Sizing unit and straightener ??Friction saw ?? Run-out table
3. TECHNICAL DESCRIPTION AND SPECIFIATIONS
Uncoiler
This equipment is used for unwinding the coil.
Type | Double Mandrel |
Capacity | Max.3000kg |
Coil Specification | Strip width:200mm-520mm Coil ID:508mm&610mm Coil OD:800-1500mm Max |
Main Base Turning | 180°Rotation by manual |
Brake | Pneumatic disk brake type |
Expansion | By Manual |
Baffle device | Include |
Lubrication | Manually by grease gun |
Shearing & butt welding machine
In this unit the trailing end of a proceeding coil and the next coil passing through the mill are trimmed parallel by shear and then butt-welded together, these actions being controlled automatically or manually or by push buttons on the control board.
Shear Cutting: | By Hydrualic |
Strip head and tail center: | by manual |
Strip Width: | =520mm |
Strip Thickness: | =3.0mm |
Welding machine: | by Manual |
Spiral accumulator
The reverse loop accumulator is installed between the shear& welder and the forming line, Its purpose is to give enough time for feeding the new coil from uncoiler to shear & welder to cut and join end of the new coil with tail end of previous coil.
Entry(Filling) speed | 180m/min |
Exit (Line) speed | Max 100m/min, continuous operation |
Stora capacgeity | 400-600 meters |
Forming section
Shaft material: | 40Cr,HF tempering quenching |
Material of gear box: | Cast steel |
Material of bevel gear: | 20CrMnTi |
Driven stand | 7 sets |
Idle stand | 8 sets |
Gear box | 7 sets |
Horizontal roll shaft diameter: | 70mm |
Vertical roll shaft diameter: | 50mm |
Squeeze roll shaft diameter: | 40mm |
Forming Motor: | DC 55kw, 1 set |
- Buy pinch leveler And leveler rolls 1 Pieces / (Min. Order)
- Uncoilers Is Mainly Used For Supporting Strip And Folded Strip, 1 Pieces / (Min. Order)
- High-performance Uncoilers Suitable For Welded Pipe Production Line 1 Pieces / (Min. Order)
- Wholesale Various High Quality Low Carbon Steel Erw Tube Mill 1 Pieces / (Min. Order)
- Hf Staight Seam Pipe Mill, Pipe Making Machine, Tube Mill 1 Pieces / (Min. Order)
- Hf Tube Mill for Steel Welding Pipe 1 Pieces / (Min. Order)
- High tech ERW pipeline pipe is a special equipment for pressure transmission pipeline 1 Pieces / (Min. Order)
- Welcome to but the quality used and automatic slitting line from our company, a professional supplier in this field. 1 Pieces / (Min. Order)
- High Frequency Low Carbon Steel Welded Pipe Tube Mill Production Line 1 Pieces / (Min. Order)
- Welding Tube Pipe forming Making Machine Line 1 Pieces / (Min. Order)
- High Frequency Straight Seam Rectangular Pipe Tube Mill forming Production Line 1 Pieces / (Min. Order)
- CR or HR Carbon Steel Tube ERW Pipe Mill Making Machine 1 Pieces / (Min. Order)
- Round or Square Steel Tube Mill for Welded Pipe Making Machine 1 Pieces / (Min. Order)